Loire Gestamp installed its first servo-mechanical line at Navarra
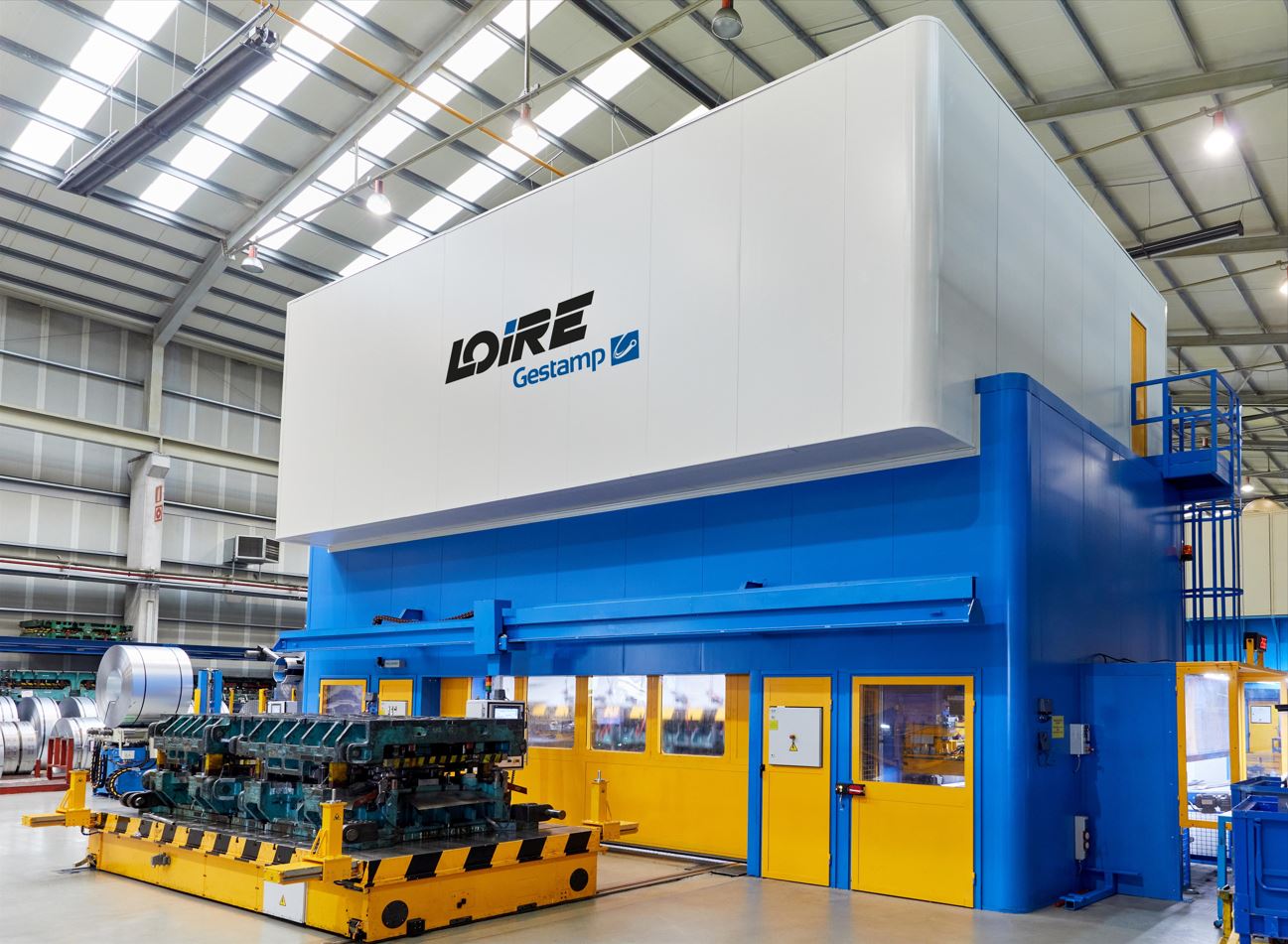
Servo-mechanical presses, a step forward in stamping
As is always the case, hybrids or subtypes are developed in every evolution. The clear example is the servo-mechanical presses, which allow programming flexibility, with a high production rate.
Loire Gestamp installed its first fully monitored servo-mechanical line at the Gestamp Navarra plant in 2020, based on the company`s latest technical developments, to ensure greater production and flexibility with lower energy consumption.
In addition, Loire Gestamp personnel have implemented INDUSTRY 4.0 on this press, as well as on the hydraulic press lines. Many press lines have been successfully monitored worldwide. This additional service provides comprehensive information through data analysis of each press line to detect alarms and possible solutions. Also, through this data analysis, LOIRE GESTAMP`s R&D department focuses on identifying and defining the main areas of improvement where higher productivity-quality is to be achieved.
Hydraulic or mechanical press?
The evolution of presses, not only in the automotive sector, has left in industrial history dozens of types of these machines, each one more precise, with one or another application. However, it should be noted that, traditionally, the two main types of presses are hydraulic and mechanical.
The basic difference is the type of drive: hydraulic presses are driven by hydraulic cylinders that raise and lower a plate on which the die, the matrix that shapes the part in the stroke, is placed, and mechanical presses are driven mechanically, for example, by means of connecting rods that transmit the movement.
Another difference between the two is that while the hydraulic presses allow maximum force to be exerted on the sheet throughout the press stroke and flexible programming, so that very complex parts can be formed, the mechanical presses exert maximum force at the end of their stroke and generally allow a higher level of production rate.